How Timely Packaging Machine Repair Can Prevent Costly Downtime
Quick and Reliable Packaging Device Fixing Provider to Minimize Downtime
In the affordable landscape of production, the efficiency of packaging operations depends upon the reliability of equipment. Quick and trustworthy repair service solutions are vital in mitigating downtime, which can result in considerable operational setbacks and monetary losses. Understanding the value of timely treatments and the function of professional professionals can change exactly how companies come close to repair and maintenance. Browsing the myriad options offered for repair solutions can be challenging. What elements should businesses think about to guarantee they are making the right choice for their operational needs?
Significance of Timely Fixes
Timely fixings of packaging devices are essential for preserving operational efficiency and minimizing downtime. In the fast-paced setting of production and product packaging, even small breakdowns can result in substantial hold-ups and performance losses. Addressing problems without delay makes sure that devices operate at their optimum capacity, thus safeguarding the circulation of operations.
Furthermore, normal and prompt upkeep can stop the rise of minor issues into significant failures, which frequently incur greater repair prices and longer downtimes. A positive strategy to machine fixing not just protects the stability of the devices yet also improves the total integrity of the production line.
Furthermore, timely repair work contribute to the longevity of product packaging equipment. Devices that are serviced quickly are much less likely to deal with too much deterioration, allowing companies to maximize their investments. This is specifically important in sectors where high-speed product packaging is vital, as the demand for constant efficiency is critical.
Benefits of Reliable Company
Reputable company play a pivotal duty in making certain the smooth procedure of product packaging machines. Their proficiency not only improves the efficiency of repair services but also contributes dramatically to the durability of equipment. Dependable provider are furnished with the technological understanding and experience necessary to detect issues precisely and carry out effective solutions promptly. This decreases the risk of reoccuring troubles and ensures that equipments operate at ideal performance degrees.
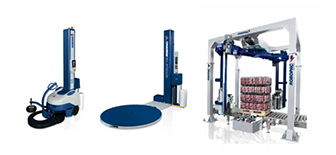
Furthermore, a reliable company offers thorough support, including training and assistance for personnel on device operation and upkeep finest techniques. This not only encourages staff members but additionally grows a culture of safety and performance within the organization. On the whole, the benefits of involving trusted company expand past prompt repair services, favorably affecting the whole functional operations of packaging processes.
Usual Packaging Maker Issues
In the world of packaging procedures, different issues can endanger the effectiveness and capability of makers. One widespread trouble is mechanical failing, typically stemming from deterioration or inadequate maintenance. Parts such as equipments, belts, and electric motors might fail, causing breakdowns that stop production. Another typical problem is misalignment, which can cause jams and unequal packaging, impacting item high quality and throughput.
Electrical troubles can likewise disrupt product packaging operations. Faulty circuitry or malfunctioning sensing units might cause unpredictable equipment habits, creating hold-ups and increased operational expenses. Additionally, software problems can hinder the maker's shows, causing operational inefficiencies.
Inconsistent product circulation Go Here is another critical problem. This can occur from variants in item dimension, weight, or form, which might affect the maker's ability to manage items accurately. Inadequate training of operators can worsen these issues, as inexperienced employees may not acknowledge very early indications of breakdown or might misuse the equipment.
Attending to these typical product packaging maker issues without delay is important to maintaining efficiency and ensuring a smooth procedure. Normal assessments and aggressive upkeep can significantly reduce these issues, promoting a trustworthy product packaging environment.
Tips for Minimizing Downtime
To reduce downtime in packaging operations, carrying out a positive upkeep method is vital. On a regular basis scheduled maintenance checks can recognize prospective issues before they escalate, guaranteeing devices operate effectively. Developing a routine that consists of lubrication, calibration, and examination of vital components can dramatically decrease the regularity of unexpected malfunctions.
Training staff to operate equipment correctly and identify early warning indicators of breakdown can also play a crucial role. Empowering drivers with the understanding to execute basic troubleshooting can stop small issues from causing major hold-ups. Furthermore, maintaining a well-organized inventory of crucial extra components can expedite repair work, as awaiting components can bring about extended downtime.
In addition, documenting equipment performance and maintenance tasks can aid determine patterns and persistent issues, permitting for targeted treatments. Integrating sophisticated monitoring innovations find out can supply real-time information, allowing predictive maintenance and lessening the danger of abrupt failings.
Last but not least, promoting open communication between operators and maintenance teams guarantees that any kind of abnormalities are without delay reported and attended to. By taking these proactive steps, services can boost functional effectiveness and significantly minimize downtime in packaging procedures.
Picking the Right Repair Work Solution
Picking the ideal fixing solution for product packaging equipments is a critical choice that can dramatically affect operational performance. Begin by examining the service provider's experience with your details kind of product packaging devices.
Next, take into consideration the provider's reputation. Seeking responses from various other businesses within your sector can provide understandings into dependability and top quality. Certifications and partnerships with acknowledged tools manufacturers can also show a dedication to quality.
Furthermore, assess their feedback time and schedule. A provider that can use prompt assistance minimizes downtime and maintains production flow consistent. It's likewise critical to ask regarding warranty and solution warranties, which can reflect the self-confidence the supplier has in their work.
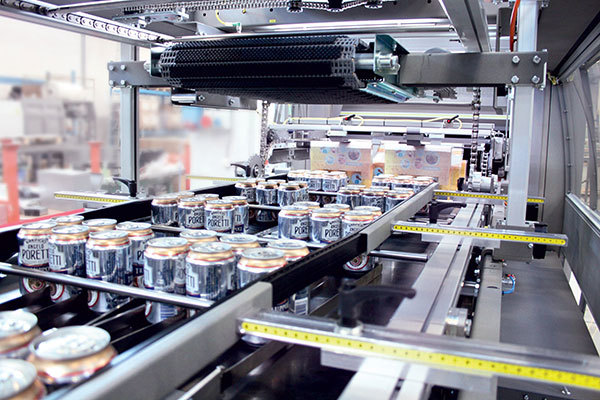
Final Thought
In verdict, the value of quick and reputable packaging equipment repair services can not be overemphasized, as find out here now they play an important role in lessening downtime and making sure operational effectiveness. Executing aggressive upkeep techniques and spending in team training further improves the durability of product packaging equipment.
Prompt fixings of product packaging machines are vital for keeping operational effectiveness and lessening downtime.Furthermore, prompt fixings contribute to the long life of packaging machinery. Overall, the advantages of involving trustworthy service providers extend past immediate repairs, favorably influencing the whole functional process of packaging procedures.
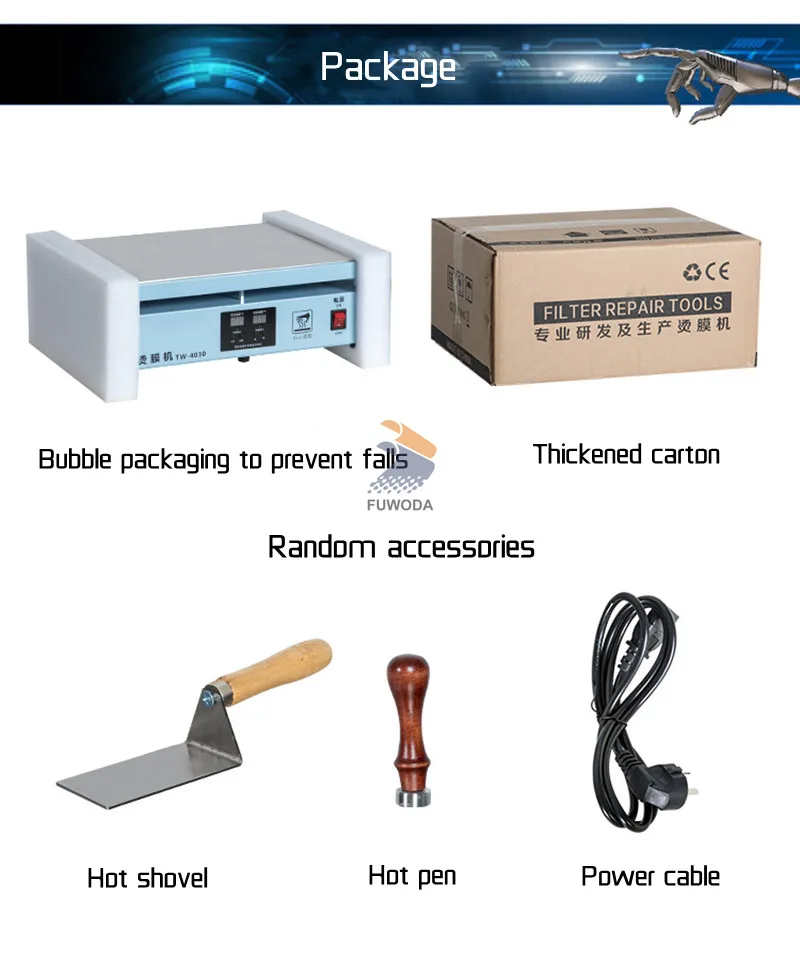